Fitting the Abrasive Tools
- Remove the battery from the power tool before carrying out work on the power tool (e.g. maintenance, changing tool, etc.). The battery should also be removed for transport and storage. There is risk of injury from unintentionally pressing the on/off switch.
- Do not touch grinding and cutting discs until they have cooled down. The discs can become very hot while working.
Clean the grinding spindle (22) and all the parts to be fitted.
Lock the grinding spindle with the spindle lock button (3) before clamping and releasing the abrasive tools.
- Do not press the spindle lock button while the grinding spindle is moving. The power tool may become damaged if you do this.
Grinding/Cutting Disc
Pay attention to the dimensions of the abrasive tools. The diameter of the hole must match that of the hub flange. Do not use an adapter or reducer.
When using diamond cutting discs, ensure that the arrow indicating the direction of rotation on the diamond cutting disc matches the direction of rotation of the power tool (see the direction of rotation arrow on the machine head).
See the graphics page for fitting instructions.
Use the quick-clamping nut (21) to secure the grinding/cutting disc without the need for additional tools.
Note: When assembling bonded grinding or cutting discs using the supplied mounting flange (17) and the quick-clamping nut (21), the use of intermediate layers is not necessary.
To secure the grinding/cutting disc, place the mounting flange with O-ring (17) on the grinding spindle (22) and screw on the quick-clamping nut (21).
Only use the quick-clamping nut (21) for grinding/cutting discs up to a maximum diameter of 150 mm.
- The quick-clamping nut (21) may be used only for grinding or cutting discs.
- Only use quick-clamping nuts (21) that are in good working order and not damaged.
- When screwing on, make sure that the printed side of the quick-clamping nut (21) is not facing the grinding disc.
- Always secure a grinding/cutting disc using only the quick-clamping nut (21) supplied.
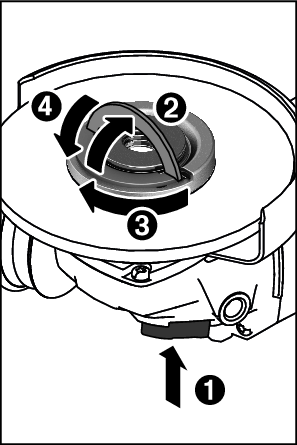
Press the spindle lock button (3) to lock the grinding spindle. To tighten the quick-clamping nut (21), fold up the bar and turn the quick-clamping nut firmly clockwise. Then fold down the bar to secure the quick-clamping nut. It is not sufficient to tighten the disc along the edge.
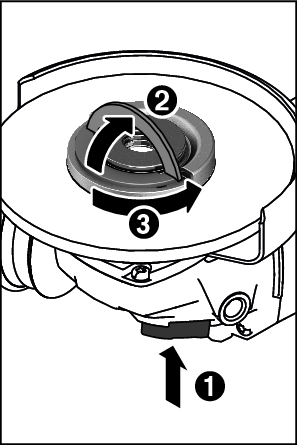
Quick-clamping nuts (21) that are properly secured and not damaged can be removed by hand. To do this, fold up the bar and turn the quick-clamping nut firmly anticlockwise. If the quick-clamping nut is stuck, do not attempt to loosen it with a tool – always use a two-pin spanner.
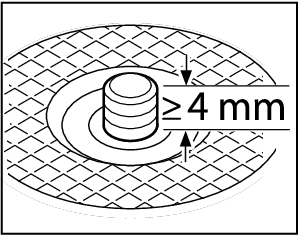
After fitting the mounting flange and the grinding/cutting disc, the free thread length of the grinding spindle must be at least 4 mm.
Ensure that the abrasive tool is firmly seated, so that it does not twist away from the spindle in the runout of the power tool.
A plastic part (O-ring) is fitted around the centring collar in the mounting flange (17). If the O-ring is missing or damaged, the mounting flange (17) must be replaced before operation can resume.
- After fitting the abrasive tool, check that the abrasive tool is fitted correctly and can turn freely before switching on the power tool. Make sure that the abrasive tool does not brush against the protective guard or other parts.